Kidyaks |
|
By Marc Bourassa - North Andover, Massachusetts - USA |
Please find attached some photos of our Fall father/son boatbuilding project; 2 kidyaks for the boys! I have built 2 boats prior to this, both stitch & glue, including the Glen-L 14’ Power Skiff, and this Kidyak design is a real breeze so far. My boys are 9 & 5, and they are able to do a lot of meaningful work on the boats. I’ll keep you updated on our progress – we’re looking to splash before Halloween!
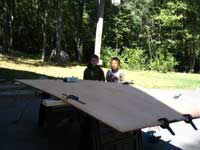 |
Ready to cut plywood. Note the grim determination on the faces of the team.
(click images for larger views) |
|
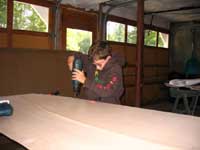 |
Alex Drilling stitch holes in the bottom panel. We overlaid 2 pieces for each cut, producing panels for both boats at the same time. |
|
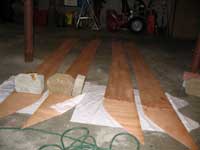 |
Sides butt-joined and curing in the garage. |
|
We’re using 4mm Sapele for the sides and 6mm Okume for the bottom & bulkheads. We’re also using 4/4 stock mahogany for the coaming and keel. Cost is a bit more, but we’re planning to bright finish a lot of the boat, so the mahogany will provide a beautiful look. I want my children’s grandchildren to paddle these boats.
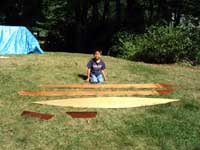 |
Jack posing with the finished panels of his boat. We’re epoxy coating one boat before stitching/taping and one boat after, to see which method is more efficient. |
|
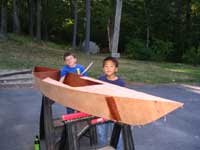 |
Here’s Alex & Jack with one of the boat hulls all stitched up (that’s my beer, by the way). The sides and bottom matched up very nicely. The forward deck is just placed on top for show. |
|
 |
Lookin’ good with the proud builders (there’s a sneak peek at my Power Skiff in the background). |
|
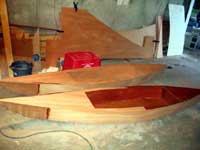 |
Next Steps: Fillets & tape. |
|
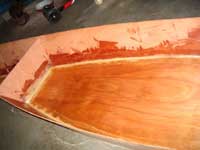 |
Here’s the hull of Alex’s boat filleted & taped. |
|
We used the “wet on wet” method, simultaneously building the fillets, laying on tape and wetting out. We find this to be more efficient; less epoxy usage, faster to complete and less sanding required after the fact.
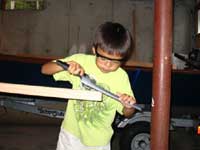 |
Jack spends some quality time with the skeg, rounding off the ends. |
|
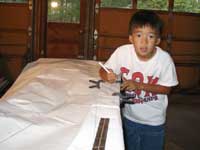 |
Tracing the last pieces. |
|
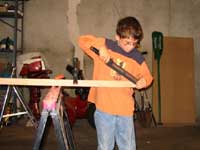 |
More skeg rounding. These may be the most over-engineered components in boatbuilding history! |
|
Note the thick coating of mahogany dust covering the floor and almost everything else in the garage. This makes my wife unhappy. I am sorry about that. Sort of.
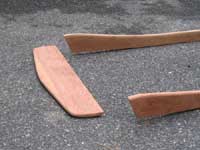 |
Coaming and front splash formed. |
|
I bought a 3/4” by 4” piece of mahogany decking for $6.00 at the local builder’s supply. I bonded 2 pieces together to get the width I needed for the front. A little work with the plane, rasp & sander resulted in some pretty nice-looking trim, I think.
CHAPTER II: COMPLETING THE ALEX B!!
Well, it’s the end of January, and we’re finally finished with one kayak, the Alex B. We decided to forge ahead and complete one of the boats, the theory being that we would learn more from our mistakes and apply our learning to the next boat. So let’s pick up where we left off, about 50% done with about 90% left to go!!
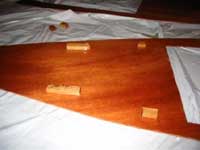 |
We glued blocks in place under the decking to allow us to install hardware later. |
|
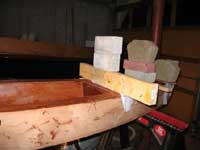 |
Installing the decks. Not very elegant, but effective. Note that we have stitched the decking along the open cockpit area to afford a tight fit. |
|
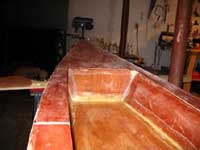 |
Decks installed and underside taped. |
|
For this step, I flipped the hull upside down onto sawhorses, then got on my knees, stuck my head in the cockpit (wear an old hat) and installed the tape on the underside of the decking. Probably the most difficult and messy part of the job.
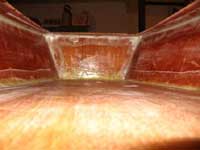 |
Another view of the taped cockpit. |
|
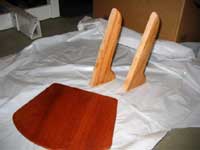 |
We decided that a nice seat would make a pleasant addition to the boat, so I fashioned a back from some oak stock and a piece of scrap sapele. |
|
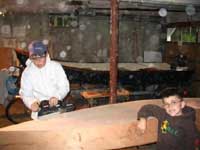 |
Here’s Alex and his good friend Ian sanding and preparing the hull for taping. |
|
Alex’s friends were a continuous, reliable source of cheap labor; they couldn’t wait to get their hands on the tools and help out. I’m not sure what caused the bubbles in this shot. It’s an old camera and may have a Lawrence Welk setting.
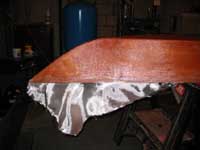 |
A shot of the glassed hull. Next time I will lap the cloth over the top of the deck about 1” or so, eliminating the need for taping that area. This will save time and provide a neater finish. |
|
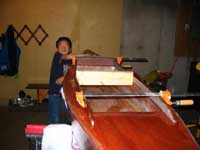 |
Here is Jack assisting with the installation of the coaming. |
|
I must say I’m rather proud of this technique. I press fitted a 2 x4 into the widest part of the coaming, then bent the longitudinal pieces around it, forming a curve that followed the sheer of the decking exactly. I held the assembly in place with the bar clamps shown, then glued it all into place. Be sure to cover the 2 x 4 in plastic to avoid bonding the coaming to it!
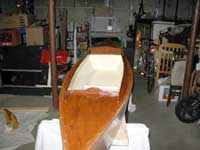 |
And down the stretch they come. |
|
We have sanded and faired the cockpit, then primed and painted it. We have also installed the other pieces of the coaming and slapped a coat of varnish on it. Altogether we applied about seven coats of varnish (I lost track of the exact number. Must have been the fumes).
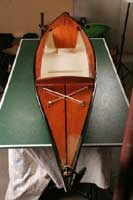 |
The completed Alex B. I used 3/16” Fine Line tape to mask for the deck perimeter and center line. The hardware includes a brass pad eye in the bow, as well as some smaller eyes for the deck bungees and stern. I also installed toggle handles for easy team carrying. The stop that you see on the bottom forward of the seat back is to accommodate a seat cushion – illustration below. |
|
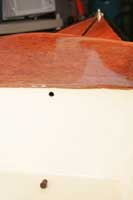 |
I drilled a 3/8” hole in the forward and aft bulkheads and fitted a rubber bung into each to allow for ventilation. |
|
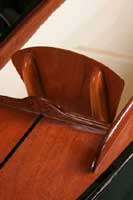 |
Some additional views of the finish work….. |
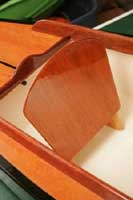 |
|
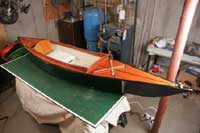 |
Note the flotation cushion in place for added safety and comfort. |
|
As you can well imagine, this project has been enormously rewarding. We’ll get right to work on the Jack B, and will no doubt be having some serious fun in the spring. I’m also going to try and get in a 2 person kayak so my wife and I can paddle along (although I’m quite sure that this will detract from the appeal for Alex & Jack).
The project is very straightforward, and the plans are excellent. The youngsters can participate in most of the process; I did not let them handle epoxy or epoxy sanding. The key is to bring them in for small steps that have a big visual impact.
NEXT UP: COMPLETING THE JACK B.

More articles about boatbuilding and boating with kids:
|