Part One - Part Two - Part Three
Editor's note: These remarks were taken from a lively discussion on the Duckworks forum. We post Michael's comments here as he speaks from a position of extensive experience.
I'm, by nature, a very cautious person in my building and design work. I'd never say epoxy is the ONLY way, but it makes sense - though I get sick of the mess and the general stickyness. But it has advantages of gap filling (important for boat longevity and low maintenance).
I try to keep a hold of the larger view, in terms of seeing what really works for large numbers of boats. Happily, I've been involved in racing, the wooden boat revival and cruising boats, including many years doing maintenance and repainting. All in quantity, so it is possible to make some sense of the general trends. Also over, what is now sadly/nostalgically, a reasonably long period.
Racing since 1972. Involved in maintenance and painting as my work from 1981 to 1999. Seeing the changes epoxy made to our lightweight wooden boat classes in Australia from about 1980. Assisting home builders with boatbuilding materials and advice since 1989.
I'll give some specific examples of things you can see from the numbers.
ENCAPSULATION: Where each piece of wood in the boat is sealed on all sides with epoxy. Not just cold moulded with epoxy between the layers as well
To protect plywood the story is the same as every other wooden part of the boat. It needs epoxy on all sides for the coating to be an encapsulation of the part. If this is inconsistent then the capsule is broken and you don't get the protection.
TELEGRAPH POLES: Telegraph poles assume the surface is going to crack, but if the pieces remain firmly attached there's little change in strength from longditudinal splitting. Same for house frames.
They do say as long as the crack is smaller than your fist :)
So maybe the approach works if you build the boat out of telegraph poles and have pumps ;)
EPOXY STOPS LIQUID WATER BUT NOT WATER VAPOUR - BUSTED
WEST make the argument - no air, no water, then no life - in terms of preventing rot. But how effective is the barrier?
The Sabre class Dinghy in Australia is 12ft long and 90lbs so it hits at the low end of our normal hull weight range of 8 to 10 lbs per foot of weight. There have been close to a couple of thousand. I was involved in sailing for a couple of seasons and helped in boat, foil and building development for about 5 years. I know many people who sail in the class including several serial builders.
Before epoxy the boats would put on about 6 to 8 pounds of weight during the sailing season. That's with every attempt to keep the things dry and very soundly built with no leaks into the tanks. The hullweight limit is quite low so it actually impossible to build a boat to the minimum hullweight with full epoxy sealing coats. It will always end up about a kilogram (2.2lbs) over.
BUT ... during the sailing season the epoxy sealed boat won't pick up any measurable weight. So you are 4 to 6lbs better off.
Now this weight can't be just where water touches the hull. Liquid water just doesn't spend enough time in contact with the hull each week (even with after sailing beers) and the boat is hosed down and carefully mopped and dried. The likely problem has always been inside the tanks with the difficulty of really drying out the air. Any water in the tank is small in quantity and might just wet part of the floor area.
Vapour is the culprit. It is also the reason that not all epoxies are equal. The quality epoxies are "high solids" which means no thinner is added. Where thinner is added (cheap epoxy and CPES the thinners evaporates from the epoxy matrix leaving it porous ... on a molecular level. Where the largish solvent molecules evaporate from ... that leaves enough space for water molecules to go through the matrix.
As soon as you have lone water molecules wandering through ... they are behaving like vapour ... not like liquid water any more. Not enough of them to make the surface tension effects really appear.
Anyway .. that's my experience. Not just one or two boats but over 10 or so classes which still have ply boats over lots of years with total number of boats in wood epoxy probably around the 500 mark
To be more techy, here's a reference to real tests - note the first sentence - there's more data on preventing water vapour than there is on preventing liquid water intrusion.
Before anyone goes too far with the statement in the article about how moisture content goes up and up with epoxy as well ... remember the samples are fully surrounded by the test environment, but boats are usually dryer on the inside. WEST claims (and they are one of the few to have done extensive testing) that the wood stabilises at pretty much the same moisture content as dry stored timber in the local environment - too dry to rot.
Someone said the coating has to encapsulate. That's correct. Fittings and fastenings need to be dipped in the dreaded 'pox before running them in.
If it did encapsulate and water gets in to any extent then an inferior epoxy has been used that was solvent based or not enough coats applied (three coats is regarded pretty failsafe).
Here is WEST doing a review of some of their older boats.
This is very much in line with my experience over boats big and small.
I've pulled a lot of polyester/glass off boats in strips and the wood is saturated underneath (not a vapour barrier) - never the case with epoxy ... but we've always made sure people understand how to use it!
My boat experience comes from the pre-epoxy era of racing dinghies. Initially the boats I owned were second hand, glued with urea formaldehyde or resorcinol glues assisted by ring nails, polyester/glass taped and painted with enamel or varnished.
The average maintenance for most of us sailing such light heavily loaded boats was pretty serious. The first couple of years they were fully watertight, but then a few leaks would start to appear in year three. By year 4 or 5 there would be substantial leaks and the boat would no longer be competitive. The paint would have started checking over the more heavily curved areas.
You could strip off all the paint, rip off the glass tape (polyester either holds on or doesn't stick well at all - usually a mix of both on one boat), retape it, repaint it. Time consuming, dirty, expensive.
Post epoxy you can be sure of no leaks ... ever. Maintenance was down to a light sand every five (or often every 10) years providing the boat was kept out of the weather and the sun.
This is experience over thousands of boats with information shared by various class organisations.
I worked for Duck Flat Wooden Boats in Adelaide from 1989 to 1993. I've continued working in the same industry and still have contact with people and their boats from the early days.
Can an amateur do a good enough job with epoxy to get the low maintenance and longevity?
Absolutely.
Over the couple of hundred boats I still know about and the thousands I kept track of for some time - the difference between epoxied and non epoxied boats is chalk and cheese.
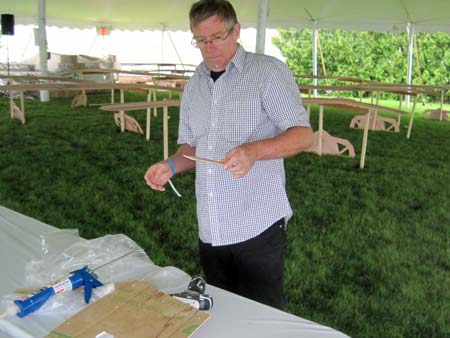
Can an amateur do a good enough job with epoxy
to get the low maintenance and longevity? Absolutely.
Now 20 years later all the boats I am still in contact with are going very nicely in good condition and less maintenance.
Several Goat Island Skiffs from the early '90s have had light maintenance of the varnish at the 10 to 15 year point. Two pot polyurethane paint over hulls is still immaculate.
I felt that epoxy was too expensive and a bit weird in the early days designing and building boats so my original BETH (design #1 1980) was cut up last year - the paint and varnish (no epoxy) had failed to protect the boat - the outside was a real mess of cracking veneers. She was outside but under a good cover ... just the same as the Goat Island Skiffs in the para above.
Sigh - everything I did for work was epoxy coated ... but I was a bit too inflexible for my own boats in my early days as a designer/builder.
|